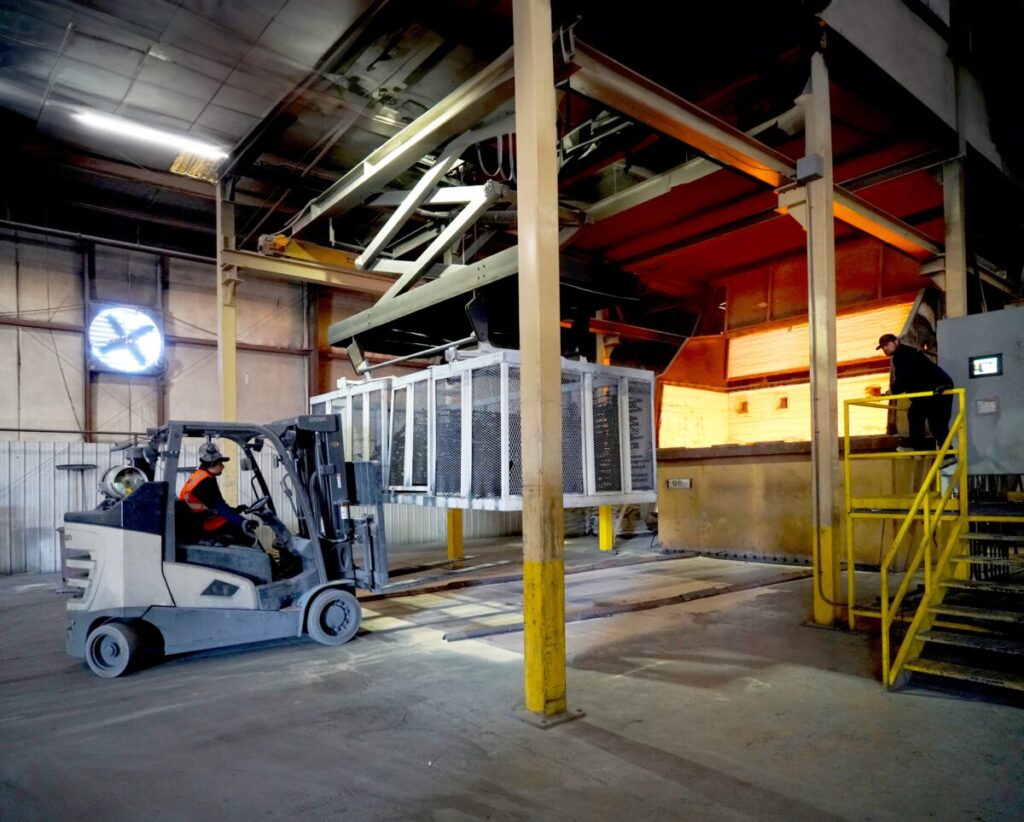
PPS’ acquirement of the former Lee Industrial in Huntsville, Alabama included a bonus—an unusual paint stripping machine called a Dinamec Systems Fluidized Sand Bed. Looking like something out of a medieval painting, the sand bed uses heated sand to strip the paint from metal parts much faster and efficiently than the standard oven and even a chemical dip, although each of the more traditional methods still has its place.
Operations Manager Dillon Campbell, who worked for Lee Industrial for five years before the PPS acquisition, said that while the ovens use heated air to remove the old paint, the sand bed uses sand as the heat medium. He said the sand bed will clean roughly 2,000 to 3,000 pounds of parts at a time and the cleaning cycle only takes a little more than half an hour; the ovens take four to five hours to clean a load of parts.
“We have the ability turn around an entire stripping job in two hours,” Campbell said. “We have one customer we run two times a day. The truck shows up early in the morning and PPS can run two truckloads of parts per day. The sand bed has a quick turnaround time.”
It’s also environmentally friendly because the sand can be reused again and again for roughly six months to a year before it needs to be replaced. Campbell explained the sand sits on top of a layer of gravel, and those layers rest over tubes of gas. The gas rises though the sand and gravel and ignites into brilliant flame when it reaches the air.
The painted parts are immersed into the flaming sand bed. Campbell said the vaporized paint is filtered from the air escaping the sand bed and its emissions are clean. The sand bed’s major drawback, however, is it’s not able to clean tubular parts because the sand is nearly impossible to remove from them, and tubular parts are cleaned in the ovens.
Campbell said PPS-Huntsville’s business increased dramatically following the acquisition because the plant added a second shift. “It’s really nice having the second shift because there’s no stress about my first shift guys having to get everything done by the end of the shift,” he said. “Anything that’s held over can be relegated to the next shift. As long as it’s done by 5 a.m. the next morning, that’s all that matters.” Campbell said there’s also a smaller third shift team to clean and prepare the plant for the next day, as well as finish up any odds and ends from the other shifts.
Business is expected to continue to increase as the Huntsville plant installs a second, smaller Fluidized Sand Bed, at least one more oven and a complete chemical dip process, similar to the other PPS facilities. Campbell expects to add another 10 to 15 jobs by the time all the new equipment is installed and operational this summer.
After working for the former Lee Industrial for several years, Campbell was understandably skeptical when he learned MPW and PPS would acquire the company. He’s pleased to report that life at the plant has only improved since the acquisition.
“One thing I like about MPW is they kept all the Lee Industrial employees. My whole team is still here. Nobody’s left the company,” Campbell said. “It’s really enjoyable and beneficial to keep my same team intact.” He said his team members encouraged their friends to hire on as well. “Everybody works great together. It makes a really good work environment, and everybody loves it,” he said. “They’re happy!”